- Home
- Sponsors
- Forums
- Members ˅
- Resources ˅
- Files
- FAQ ˅
- Jobs
-
Webinars ˅
- Upcoming Food Safety Fridays
- Upcoming Hot Topics from Sponsors
- Recorded Food Safety Fridays
- Recorded Food Safety Essentials
- Recorded Hot Topics from Sponsors
- Food Safety Live 2013
- Food Safety Live 2014
- Food Safety Live 2015
- Food Safety Live 2016
- Food Safety Live 2017
- Food Safety Live 2018
- Food Safety Live 2019
- Food Safety Live 2020
- Food Safety Live 2021
- Training ˅
- Links
- Store ˅
- More
Advertisement
Featured Implementation Packages
-
SQF Implementation Package for Pre-processing of Plant Products - Edition 9
This comprehensive documentation package is available for immediate download and... more
-
Consultants 10 Site License Package
This is a great value package for consultants providing GFSI implementation serv... more

Product Withdrawal & Recall Survey
Jul 08 2015 10:21 AM | Simon
product recall product withdrawal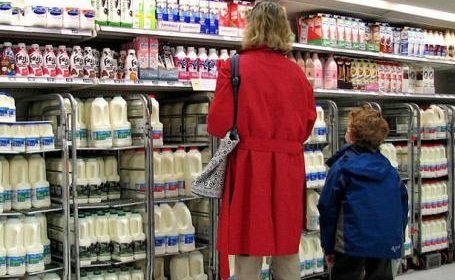
Link to the Full Survey Results
Main Findings:
- Over half of the 70 respondents had experienced at least one product withdrawal or product recall within their business
- Over 1/3 of these withdrawals or recalls were due to either microbiological contamination or undeclared allergens
- The main triggers for initiating the withdrawal or recall were:
- Quality Test Result
- Other Trigger
- Regulatory Inspection Finding
- Food Test Result
- Consumer Complaint
- The majority of respondents reported that their traceability system and the withdrawal / recall process was both effective and efficient
- In 1/2 of the cases the total cost of the withdrawal or recall was less than $10,000 USD, however:
- 8 cases the cost was between $100,000 and $500,000 USD
- 2 cases cost was between $500,000 and $1,000,000 USD
- 1 case the cost was greater than $1,000,000 USD
- Consumers were harmed in one case only
- The vast majority of respondents stated that they did not have another incident of the same nature
Although the survey is limited in scope it does offer some insight into the causes and costs of recalls and withdrawals. The costs alone show the value of striving for food safety perfection, in reality a zero defect rate is not possible and personally I would have expected almost all food respondents to have conducted a withdrawal at some point.
There is sometimes confusion between Product Withdrawal and Product Recall yet there is a distinct difference, which is explained quite well by the IFS Standard.
Product Recall: "Recall" shall mean any measure aimed at achieving the return of dangerous product that has already been supplied or made available to consumers by producer or distributor.
Product Withdrawal: "Withdrawal" shall mean any measure aimed at preventing the distribution, display and offer of a product dangerous to the consumer.
The key word here is “prevention”. Withdrawal is a proactive and preventative approach to removing harmful goods from the supply chain before it is too late and consumers are put at risk. Although a withdrawal is undesirable it is a right and proper business decision to instigate one from both an ethical and financial point of view. Yes it disrupts the supply chain however, enlightened customers see it as a “good thing” as it protect their customers (the consumers) and demonstrates that the supplier’s crisis management procedures are “real” and form part of a fully functioning and effective Food Safety management System.
As the survey did not distinguish between withdrawal and recall we cannot say what proportion were for withdrawal or recall and therefore we cannot conclude whether the results are a good or bad thing. That said things can and do go wrong and it is how we correct the problem and prevent reoccurrence that is of most importance. It is encouraging that the vast majority of respondents did not experience a repeat incident for the same problem.
You can find information on the latest recalls at the following links:
Please feel free to add your comments below.
6 Comments
I am new here working in a food processing industry and currently working on our FSMS ISO 22,000.. I am grateful for the articles here and hope to contribute in the topics but i am not informed on how to do it. any guidance will be highly appreciated
What's the basis for product recall? Is it concerning quality safety issues or just food safety issues?
Both I would say, if it can affect the consumers health.
Reason for product recall involving food safety issue is very clear to me. How about for quality issue to be the reason of product recall? Can you give me an example?
How about if a food product has a heat seal lid and the lids were found to have minute holes put into them during manufacture. The function of the lid is to provide a tamper evident seal of the food product. If it were deemed that the holes in lids may negatively affect the shelf life of the food product and it may spoil earlier than the stated date. It may be no risk of health to the consumer as they would know the product is spoiled and also it would not contain any pathogenic bacteria, but it is not a good thing, so a recall is initiated.
This is a really good poll. Ever think of doing another?