- Home
- Sponsors
- Forums
- Members ˅
- Resources ˅
- Files
- FAQ ˅
- Jobs
-
Webinars ˅
- Upcoming Food Safety Fridays
- Upcoming Hot Topics from Sponsors
- Recorded Food Safety Fridays
- Recorded Food Safety Essentials
- Recorded Hot Topics from Sponsors
- Food Safety Live 2013
- Food Safety Live 2014
- Food Safety Live 2015
- Food Safety Live 2016
- Food Safety Live 2017
- Food Safety Live 2018
- Food Safety Live 2019
- Food Safety Live 2020
- Food Safety Live 2021
- Training ˅
- Links
- Store ˅
- More
Advertisement
Featured Implementation Packages
-
BRCGS Food Safety and Quality Management System for Food Manufacturers - Issue 9
This comprehensive yet simple Food Safety Management System Package contains EVE... more
-
SQF Implementation Package for Food Manufacturers - Edition 9 (2022 Update)
This comprehensive documentation package is available for immediate download and... more

SQF Edition 9 Updates and Compressed Air Monitoring - what you need to know
Apr 05 2021 04:00 PM | Simon
SQF Safe Quality Foods Edition 9 compressed air testing compressed air safety compressed air quality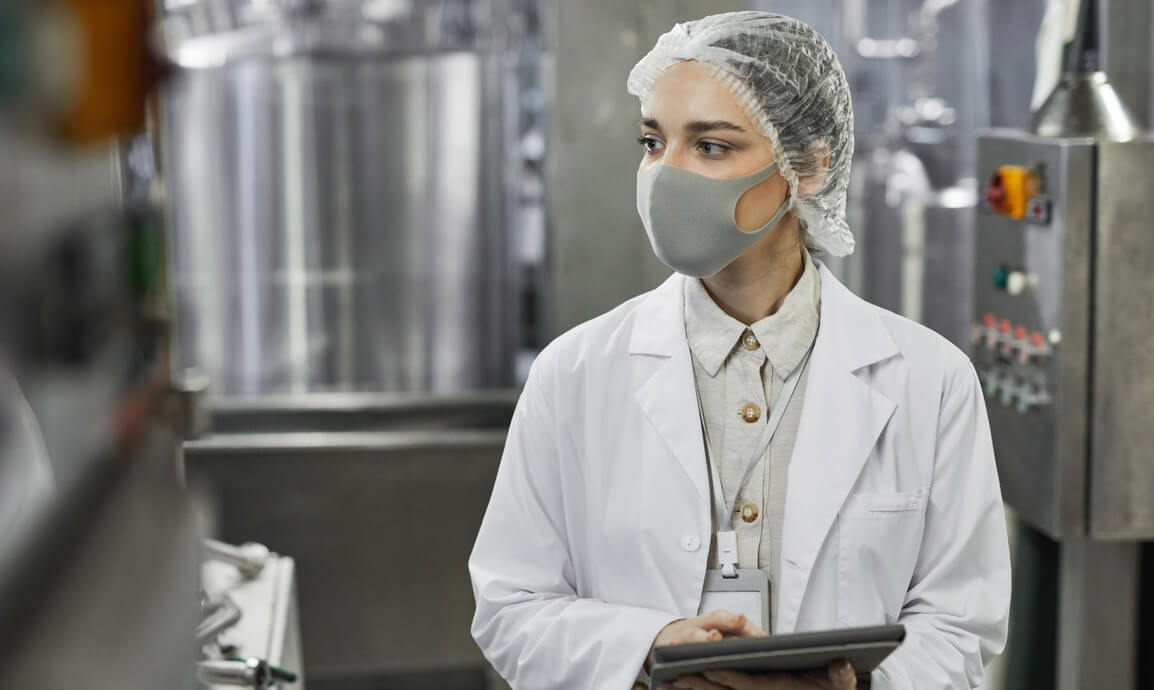
CHANGES TO SQF CODE
SQF Edition 9 comes with several enhancements and improvements to the code structure, methodology, and technical requirements. Below are the relevant compressed air and gas updates and how they pertain to the health of your compressor system and quality system alike.
SQF Edition 9:
The new addition in Module 11 states, “The frequency of analysis shall be risk-based and at a minimum annually.”
- 11.5.5.1: Compressed air or other gases (e.g. nitrogen or carbon dioxide) that contact food or food contact surfaces shall be clean and present no risk to food safety.
- 11.5.5.2: Compressed air systems and systems used to store or dispense other gases that come into contact with food or food contact surfaces shall be maintained and regularly monitored for quality and applicable food safety hazards. The frequency of analysis shall be risk-based and at a minimum annually.
Because manufacturing facilities vary so dramatically in their needs, procedures, systems, and workflows, it is critical for each to assess their individual risks. A compressed air risk assessment is a great place to start. Risk assessments account for everything from system age, to piping distribution, to filtration and dryers. Knowing where your system stands, what its limitations are, and how it could contribute to contamination can help determine the frequency and stringency of analysis.
Annual testing, at a minimum, allows manufacturers to understand their system at that point in time. More frequent monitoring allows users to create a trend analysis and understand how seasonal changes, maintenance, and other factors can affect the quality of their compressed air or gas. Of course, each facility has unique needs and risks, but the annual requirement of analysis helps to set a minimum benchmark for manufacturers.
Appendix Additions:
In appendix 2, users will find this definition of compressed air monitoring:
- A program that includes particles, water, oil, microorganism, and gases in compressed air and other gases. A verification of effectiveness of compressor maintenance and filtration a management facility has in place.
Leaks in distribution piping can provide contaminants a way to infiltrate the system. Maintenance without proper purging can introduce contamination into a system and should be considered a potential source of risk. Additions or changes to a system may leave the piping or valves vulnerable to contamination as well. Trace Analytics recommends sampling after any major repair work to ensure that the air quality has not been negatively impacted. If changes are made to a system and the system is not effectively purged, contaminants like particles, water, and oil can be left behind. Without proper monitoring, contamination could remain in the system, and if left unchecked, could impact the end-product.
WHO IS IMPACTED BY THESE CHANGES:
SQF Edition 9 has expanded and modified codes from previous editions. This change has introduced compressed air monitoring to some codes where it previously hadn’t been included. Compressed air requirements can be found in:
• Food Manufacturing
• Pet Food Manufacturing
• Animal Feed Manufacturing
• Animal Product Manufacturing
• Dietary Supplement Manufacturing
• Storage & Distribution
• Manufacturing of Food Packaging
If your facility falls into any of these categories and you use compressed air in your processes, you will be required to monitor your compressed air and gas systems at least annually (or more frequently based on your risk assessment) to ensure product safety.
WHAT TO TEST FOR:
SQF Edition 9 points to particles, water, oil, microorganisms, and gas testing for manufacturing facilities. Each facility is unique and has individual requirements, so it is essential for each user to conduct a risk assessment and compare with published standards, like ISO 8573, to choose the right purity levels for their systems. Higher risk end-products may require more strict purity levels. Some end-products may require strict particle testing, but have lower limits for water vapor.
It is also important to consider the capabilities of your system and ensure that your purity classes are achievable and appropriate. For example, black iron pipes are going to have a great deal more rust accumulation than stainless steel pipes. Systems with refrigerated dryers are going to have more moisture than systems with desiccant dryers.
ISO 8573 is an international compressed air standard that provides purity classes for particles (viable and nonviable), water, and total oil, allowing users to choose the appropriate ranges for their use. This standard can be used as a “common language” between users, laboratories, and compressed air system suppliers.
Particles:
Particles can be categorized as viable and non-viable. Viable particles are microorganisms, which will be discussed below. Non-viable particles are characterized by their size, shape, transparency, color, and material. They are of great concern to many manufacturers. No one wants to find metal shavings in their coffee grounds. Metal shavings, rust, bits of tubing and plastics are all examples of particles that might be found in a compressed air system. ISO 8573 designates size ranges with limits for each purity class to help manufacturers ensure that their filtration systems are functioning properly. If your point-of-use filter is supposed to filter particles size 0.3um and up, and your compressed air tests reveal particles sized 0.5-5, then you will need to troubleshoot your filtration and distribution lines after filtration.
Water:
Water in compressed air systems is concerning as it often leads to much bigger problems. Excess water can cause piping to rust, producing particles. This contamination can also create a breeding ground for dangerous microorganisms and saturate filters, rendering them useless. ISO 8573 offers 6 purity classes to accommodate users with either desiccant or refrigerated dryers.
Oil:
Oil vapors and oil aerosols together are known as Total Oil. Stricter limits require both aerosol and vapor testing combined. In less strict classes, oil aerosol alone can be monitored. Depending on your risk levels, you can choose the appropriate class for your system. Even if you have an oil-free compressor, maintenance oils, oils from cleaning supplies, and vehicle exhaust can infiltrate the system. It is not enough to simply replace your compressor with an oil-free one. If you’ve previously used a traditional compressor, there could be oil left in the pipes or distribution system. Regular monitoring helps ensure oils are not impacting your end-products.
Microorganisms (Viable Particles):
Viable particles, or microorganisms, can be hugely detrimental to your end-products, bottom line, and reputation. Contamination from microbes like Listeria, or Salmonella should be monitored for regularly if manufacturing consists of dairy products. Microbes can live in compressed air systems, particularly if these systems are contaminated by oil, particles, and water. These dark, wet breeding grounds can put products at risk. ISO 8573-7 recommends testing with an impaction sampler and incubating contact plates for a minimum of 10 days. Some companies may have specific indicator microorganisms that they are concerned about and need to do further identification.
HOW TO SET UP A MONITORING PLAN:
Setting up a monitoring plan is an important part of ensuring the quality of your compressed air system and meeting your certification requirements. SQF Edition 9 mentions particles, water, oil, microorganisms, and gases as contaminants to monitor. Using ISO 8573 purity classes along with a compressed air risk assessment, a user can determine how strict their limits should be.
Where to sample:
A common question from manufacturers is where to take the samples. Results from your air samples should be representative of their use on the product. If your compressed air directly impacts your products, you’re going to want to test at the point of use. Tests at the compressor can help users understand the quality of the air at the start of the system. Testing can also be performed midway through the line to understand the impact that the distribution system may have on the quality of that air.
Number of Samples:
The number of samples is also one that must be determined by the manufacturers. If you have 20 points of use, you may want to test them in rotating percentages. Testing 25% of the points of use quarterly could be an appropriate and manageable way to test each point annually. This would dictate only 5 samples per quarter. Some users may choose to test each point of use that impacts end-products. Others may choose to test at the compressor and then at the end of the line only. While a single test point does meet the minimum requirement, it hampers the ability to perform seasonal trend analysis.
Frequency of sampling:
It’s then necessary to consider how often testing should take place. SQF Edition 9 cites annually - at a minimum. Many manufacturers choose to test quarterly or semi-annually to build a trend analysis and see how their system changes over time, reacts to maintenance schedules, and handles seasonal changes.
Each facility is unique and each monitoring plan will be as well. Depending on the risk levels, the type of system, and the usage of the compressed air, a users’ monitoring plan should fit their needs. Third-party, ISO 17025 accredited laboratories, like Trace Analytics, LLC can help implement a monitoring plan, schedule testing, and provide reliable and expedient air quality results.
CONCLUSION
Preparing your compressed air system for the new Edition 9 improvements means your facility won’t be left unprepared. With the release of SQF Edition 9 comes the opportunity for manufacturers to address their quality systems, risk assessments, and monitoring plans for their compressed air systems. With added guidance from SQF, users can determine what contaminants to test for, how often to test them, and create a plan to ensure they maintain appropriate levels of quality year-round. For more information on compressed air testing, please contact the experts at Trace Analytics, LLC.
512-263-0000 ext 5 | sales@airchecklab.com
By Jenny Palkowitsh, Trace Analytics, LLC
References:
Chuboff, L. (2021, March 05). Sqf code edition 9: What's changing and how to prepare. Retrieved March 10, 2021, from https://www.sqfi.com...how-to-prepare/
Sqf code downloads. (2021, January 12). Retrieved March 01, 2021, from https://www.sqfi.com...on-9-downloads/
0 Comments