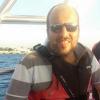
Best Answer Ehab Nassar , 23 December 2015 - 09:22 AM
So as I understand you are receiving some items packed in a glass containers ( like jam for example ) , also you had other items are packed in carton display , plastic bag ,... and so on .
I do not know if you have a raw ingredients ( like wheat flour , rice ,..) , herbs or fruits , also do you have some items to be repacked or your facility just receive and distribute only.
According to the above understanding I think that :
- You do not have to register the items which packed in glass policy , it is already in your inventory .
- Yo can only add in your glass policy handling of products in case of glass breakage .
- All glass breakage cases should be documented by time , date , location and quantity also the corrective action must be documented ( the anchor point of the corrective action is to give evidence that there is no probability of glass splinters contamination , it could be for examples visual inspection of the area , clean the area and using vacuum cleaner to swap all glass splinters from the our packaging layer of other items then assuring it is not passing through it to the inner packaging .
- Any inventory loss / difference justified that it is due to breakage must include a the required document .
- If it is possible make a section for all products with glass packaging together away from the other , however if it is not applicable you need to make a sorting in the racking ,so that reduce the risk or glass splinters in case of breakage .
- if mixing storage used then All the items in glass containers will require that any breakage incidents should be documented and the corrective action is done as per instruction as the given example above .
( auditor can easily get this by asking for the inventory difference between received and dispatched quantities , so he can ask about the reason for the variance ) .
- Sometimes the team think that the closed products will not affected by glass splinters , you should give them a concise brief about how could glass splinters could be a risk for other products , yes it will not go directly inside but it could be on the packaging and during stripping may transfer inside the contained material .
- During dispatching ( if you are using your vehicles ) , just make the sorting a proper way , add add glass breakage inside the pre-loading or loading inspection , you can also use shrink wrapping .
Finally glass breakage policy is for controlling glass contamination ,it required to be localized as per each facility , as far it is simple and practical it will be successful.
hope this answer you query ,
Good luck ,
Ehab
