Rightly said Jean
There are few more to add on in catering industry.
- Use of seasonal vegetables for food preparation.
- Soaking of Rice / Lentils before cooking that will reduce cooking time i.e. save energy(An effective method- my mom always practice this method though we are small family)
- Keep inventory as per minimum requirement. See previous trend and find out items that block the space & money . Keep control over them.
- Don't compromise with pest control, Hygiene issues etc. As many of the industry I have seen compromise with these issues to reduce the cost better look out for alternative cost effective option. e.g. gloves v/s hand washing.
In food manufacturing industry-
- Smart use of water. e.g. water conservation by recycling, distillate collection etc(either recession or not we should)
- Save energy by conservation of steam, heat etc
- Inventory control
- Use of lights, A/c, fans etc only when required and do not forget to switch off while leaving /going outside the office.
- Focus on preventive maintenance to reduce down time during production
- Reduce paper work. make comprehensive reporting system that reduces repetitive work.
For more there is an interesting article that was published in Newsletter- 'Mindtools' in Feb 2009. Here it is-
The Thrifty Manager
Cutting Costs the Smart Way
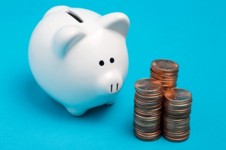
There are smart ways to trim your costs.
©iStockphoto/bluestocking
Your boss has just asked you to cut 10% from your department's budget, starting immediately.
Easier said than done, right?
As you carefully study your expenditures, you're faced with a seemingly impossible task. How do you decide what to cut? Where can you save the most money without hurting team morale, or lowering people's productivity? Should you eliminate coffee and morning donuts, or cut back on office supplies?
Most organizations have to cut costs at some point. In today's economic climate, it's more important than ever for businesses to watch their budgets, and to make sure they eliminate any unnecessary spending.
When cost-cutting is down to you, however, it can be difficult to know where to start. Cutting the right things at the right time is a delicate balancing act.
In this article, we look at some easy ways to cut your budget, and offer some suggestions to get you started.
Where to Start - Doing the Easy Things
Once you sit down with your budget, there's a chance you might feel overwhelmed. While your team might not need everything that's on the list, some items - like company vehicles or holiday parties are nice to have.
If that's the case, where do you begin?
Establish the essentials: It's important to identify the things your department absolutely cannot live without. Every business is different, of course, so necessary expenditures for one company aren't always essential for another.
Identify the 'luxuries': Once you create the list of things you can't live without, look at what's left. Some of these are probably luxury items; expenses that aren't absolutely necessary, and could easily be cut - for example, fresh flowers in the reception area.
Review your 'maybe' items: These are the things you're not so sure about. When you look at these less obvious expenditures, assess the costs against the tangible and intangible benefits of these items.
A good example might be your department's networking parties. They're fun and useful, but you might at first think that you could cut them. However, when you socialize with valuable contacts during these events, they often lead to referrals and sales. You'll therefore have to judge whether these parties are a necessity or a luxury. If you expect to gain more in sales than you spend, then it may be worth keeping parties in the budget.
Another example could be office supplies. For instance, your team might use large amounts of paper. Perhaps your company buys top-quality, expensive paper, but is this necessary? Of course, you use these items to do your work, but you could save by buying a more economical brand of paper.
Practical Budget Advice
Cutting costs is never easy, but here are some practical tips you can apply when trimming your budget:
Cross-train your staff: Many companies hire temporary workers when regular staff are sick or on vacation. But, if several members of your team are cross-trained - where they learn the skills of a job function different to their own - perhaps they can cover those duties, in short shifts, in addition to their regular workload.
Focus on efficiency: For instance, if several of your team members spend valuable time every week or month writing a report, determine whether this is really necessary. Could they spend that time on something that's more valuable? Does another team in another department create a similar report, and could you combine efforts to save time? Another benefit here is that if your team members are working more efficiently, you may be able to cut back on overtime payments.
Cut back on the work you do: Taking this further, look at the work your team does, and ask whether you need to do everything that you do. Do your 'customers' still want each and every report you produce, and each and every service that you provide? Trimming the work you do will reduce your reliance on temporary staff and overtime.
Negotiate with your suppliers: You may be able to secure discounts for early payment, or large-quantity purchases of items that your team uses regularly. Explore special deals to see where you can save.
Buy less expensive equipment and vehicles: If you're about to replace your car or truck fleet, consider purchasing less costly and more fuel-efficient models. The same goes for office equipment: used printers and fax machines are often available for a fraction of what you'd pay for new ones. Also, consider sharing these resources, and costs, with another department within your organization.
Make telephone calls over the Internet: Software such as Skype allows you to make and receive telephone calls on the Internet. As long as the person you're calling has Skype too, these calls are free. This can therefore help you to save on telephone costs.
Investigate videoconferencing or teleconferencing: If your team travels a lot for meetings, explore the costs of setting up videoconferencing or using teleconferencing instead (again, Skype offers good teleconferencing facilities). This can help you save on travel costs.
Use less costly supplies, and use fewer of them: Cutting your team's morning coffee might cause some bad feelings. Instead, why not use ceramic mugs, and stop paying for paper cups that get thrown away? If you currently buy an expensive brand of coffee, switch to one that's more economical. And how much energy can you save by turning off computers and lights at night time?
Get bids on all of your services: You might be surprised at how much you can save by shopping around for the best prices on everything from shipping to office supplies.
Cut back on magazine subscriptions: Your office or department might subscribe to industry or trade journals. These can be valuable resources for keeping your team up to date on trends and best practice, but make sure you carefully evaluate the costs against the rewards. Several team members may be able to share one subscription, and many publications offer digital versions for a reduced price.
Communicate With Your Team
If you're forced to start making cutbacks, tell your team what's going on. While no one wants to feel like they're with a company that's having financial problems, everyone knows that times are hard, and they probably don't want information kept from them. As far as you can, let your staff know what's happening, and why.
It's also important to realize that your team members are a valuable resource. They could have some really creative ideas for ways to cut costs. After all, they're the ones out there working every day. They might know of practices or expenditures that could easily be cut for the entire company - and you could ask them to come up with their own suggestions.
And, ask your team to examine where they might cut costs in their own daily routines. This could help empower them, and make them feel involved - even in a small way - in the decision-making process.
Key Points
Many people immediately think of layoffs when they hear about corporate cost-cutting. However, your people are your most valuable assets. Aim to cross-train, cut back on non-essential work, and reduce costs in supplies and business systems before you reduce your staff. Focus on making your department more efficient. And remember that even savings on small things, like turning off computers at night, can help reduce costs.
A Final Note from James
While cost-cutting is never enjoyable, I hope this article has shown you some proactive and constructive ways to help ease the process.
Our featured resources in two weeks' time focus on helping you become a better public speaker. Take our 'How good are your presentation skills?' quiz, and discover how the technique of 'centering' can help you bring your nerves under control when presenting.
Best wishes for a truly excellent week!

James Manktelow
Regards
Monika