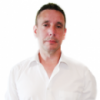
Best Answer George @ Safefood 360°, 20 June 2013 - 01:15 AM
Standard Operating Procedures are used to clearly define how a particular activity, duty, job or task is performed and are usually applied at an operational level within an organization where repeatability of a task is important. The detailed required in an SOP depends on a number of factors including:
- The importance of the procedure in regard to food safety, quality etc.
- The skills level of the person conducting the activity
- The importance of detail in terms of being audit-able
- The importance of detail in terms of being used as a training aid.
On the first point, the rule is usually that SOP's should be as detailed as necessary - where the absence of such detail would present a real risk to the safety of the product produced. This is a judgement that must be made by an experienced and competent person.
In regard to skill levels - for low skilled employees the detail of the SOP should be sufficient to eliminate any interpretation of what is required or force the employee to fill in the gaps. For more skilled personnel the detail of the procedure can be less. For example maintenance personnel will often perform complex work on machines which they qualified and trained to do. It is not necessary nor in certain cases desirable to provide detailed SOP's in these situations.
If the SOP is to be audited as part of the compliance system, there should be sufficient detail in the SOP to allow the auditor to conclude that the procedure is being conducted correctly and for training the SOP should be sufficiently detailed to allow for consistent and repeatable training and performance of the task.
In summary it really depends. In all cases it will require a responsible, competent and experienced manager to draft and define the level of appropriate detail.
George
