I think there should be something in your overarching non conforming product procedure which should cover this off. I wouldn't necessarily write something different.
So in that (and in your training) there should be a principle that if there is known contamination or found contamination that the line is stopped and someone in a position of authority and Quality is alerted. The general principle then being:
The product or work in progress is held, risk assessed, rescoped if necessary and then if necessary, rejected and destroyed with records of destruction and appropriate communication.
It should include roles and responsibilities (particularly it's important to know who has authority to release if you do), how quarantined stock is made clear to staff (e.g. labelling or on electronic systems) and what to do with product which has been made with any impacted ingredients or work in progress.
After all of that your process should capture that RCA should be part of closing out any significant incident.
I think then it keeps it vague enough so that if it was, say, a chemical contamination incident tomorrow, the process still works.
Lastly and perhaps most importantly, from a cultural point of view, it's important to train your managers that if someone does step up and say "I've made a mistake" that it's treated in good faith that it's better to make the problem visible. Issues like this lead to large rejections when people try to keep it quiet. And it does sound a bit like that happened in your case by the way it was "found".
As for avoiding glasses getting in your machinery? There are some options. Did you know for a start that safety glasses are not great for chemical use normally? The reason being they have gaps where a splash could still get in the eyes. If you want chemical safety to be assured, goggles are much better and have a strap which keeps them attached to your head.
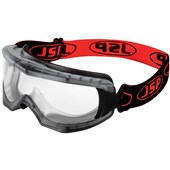
So if they're using the safety glasses kind it might be worth pointing out those aren't actually very good protection so either they're not needed or not effective...
Secondly, also I would agree that trying to design out the risk is a good idea. If your machine is say a filler or a cooking vessel has a big opening, a simple mesh of, say 1-2cm on top is enough to capture most "whoops!" moments.