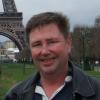
Best Answer Tony-C, Today, 06:26 AM
Hi WorkingFromWork,
I would agree that the wording isn’t great but put simply, sites develop and implement a product safety and quality management system that would cover all of the requirements of the BRCGS Global Standard for Packaging Materials Issue 7 and all the items listed are required to be in the scope of the internal audit programme.
This product safety and quality management system then needs to be audited and this system would be based on risk and previous audit performance.
I believe that this confusion comes from the changes from Issue 6:
As a minimum, the scope of the internal audit programme shall include the:
• HARA or product safety and quality plan, including the activities to implement it (e.g. supplier approval, corrective actions and verification)
• prerequisite programmes (e.g. hygiene, pest control)
• product defence and product fraud prevention plans
• procedures implemented to achieve the Standard and modules.
Issue 7:
As a minimum, the scope of the internal audit programme shall include the:
• HARA
• product safety and quality plan management system, including the activities to implement it (e.g. supplier approval, corrective actions and verification)
• prerequisite programmes (e.g. hygiene housekeeping, pest control, maintenance)
• product defence and product fraud prevention plans
• procedures implemented to achieve the Standard and modules.
Comment regarding the changes: Minor changes to this clause to clarify that the scope of the internal audit programme must include all of the site’s product safety and quality management system.
To summarise, you need to audit your product safety and quality management system and at the same time ensure that it covers all the requirements of the BRCGS Standard.
See this example of a report from BRCGS:
Kind regards,
Tony
