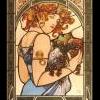
Best Answer Madam A. D-tor, 23 August 2017 - 06:23 PM
Dear Hasson 256,
To find the root cause it always helped me to ask 5 times "why?".
Example:
Deviation: improper date printing
why 1: why was the date printed improper?
answer (example): because the printer was running out of ink
why 2: why was the printer running out of ink?
answer: because it was not filled on time
why 3: why was it not filled on time?
answer: because the operator did not check the ink level on time
why 4: why did the operator not check the ink level on time?
answer: because he had no time/ forgot it.
why 5: why did the operator had no time/forgot it?
answer: because he was busy solving an equipment failure of another machine.
sometimes you need more "why?"s. Sometimes you find the solution sooner. If a question has more answers e.g. printer run out of ink and the finished product check was not conducted, than follow both answers again with why-questions.
Root causes are mostly related to: providing resources, providing training, maintenance, lack of time/ too busy staff, uninterested or unwilling staff, design of equipment, design/flow/layout of buildings.
