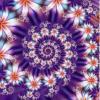
Best Answer Charles.C, 23 December 2015 - 10:52 AM
Hi vivek,
A few comments -
(1) it may depend on the FS standard, if any. I assume only safety criteria are involved.
(2) The status of the final filter IMO logically depends on a (safety) haccp risk assessment, ie is it likely that any "dangerous" objects will pass the MD but then be stopped by the final filter ?.
The answer to (2) depends on yr product / process, criterion for "dangerous" and possibly Indian Regulations as to the local (safety) assessment of yr finished product if such exist (in which case will take priority).
Just as an example, from memory Canada set > 2mm as size criterion for hazardous metallic contamination. So if the MD validatably rejects all Fe items <=2mm using, say SS 316, as a worst case reference and if only iron is considered a significant FM, then the final filter is simply redundant.
In some sectors, from an auditorial POV, it is apparently acceptable to quote an "Industry Standard" as target critical limit, ie "best practice". Presumably requires some justification though.
The USA, as per my understanding, further protect their consumers by invoking adulteration as a FM rejection possibility.
So what is yr current, validated, operational MD rejection limit for Stainless Steel ? Or perhaps yr risk-assessed metal ? If X >1mm and you can support a case for contaminants being hazardous between X and 1mm plus a likely occurrence then the final filter is CCP and the MD is redundant.
Or you could propose that the combination of "MD + sieve" is CCP for operational reasons.
Perhaps easier to quote Canada if yr MD passes the requirement and only metallic of significance and throw away the sieve. But perhaps in practice it does stop something ???
