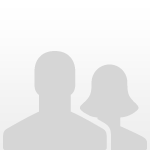
Best Answer FSQA, 07 March 2019 - 05:51 PM
I just need to find some literature about this case so I can have some back up in the eyes of the auditor. Do you have any recommendations to read for this topic (warehouse or distribution center allergen management) a little bit further or any recommendations on how to validate that I just need a really good anti spill and seggregation procedures? Like, do I need to swab the area to see any potential cross contamination?
Please see the following link (particularly page # 12/ 3.3 Allergen Clean):
https://www1.agric.g...11_allergen.pdf
You can use a verification swab of your cleaning, after an allergen spill, however, since the product is sealed and segregated i won't advise it running it after every regular cleaning of the area (cost/risk).
Hope it helps.
