- Home
- Sponsors
- Forums
- Members ˅
- Resources ˅
- Files
- FAQ ˅
- Jobs
-
Webinars ˅
- Upcoming Food Safety Fridays
- Upcoming Hot Topics from Sponsors
- Recorded Food Safety Fridays
- Recorded Food Safety Essentials
- Recorded Hot Topics from Sponsors
- Food Safety Live 2013
- Food Safety Live 2014
- Food Safety Live 2015
- Food Safety Live 2016
- Food Safety Live 2017
- Food Safety Live 2018
- Food Safety Live 2019
- Food Safety Live 2020
- Food Safety Live 2021
- Training ˅
- Links
- Store ˅
- More
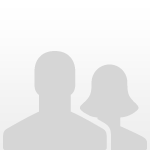
Cleaning Validation (ATP and Microbiological Test)
Started by esperanza.vivas1983, Jul 06 2022 04:29 PM
8 replies to this topic
#1
Posted 06 July 2022 - 04:29 PM
Hello everyone, I need your guidance, in a recent audit the auditor has asked me to justify how I perform the validation of cleanliness in the packaging area (Our company is only dedicated to the repackaging of processed foods).
My explanation is that our procedures are:
- Using an ATP once a week on all contact surfaces and monthly for non-contact surfaces.
- Microbiological test (Enterobacteria test) once a year on all surfaces.
The question that the auditor asked me and that I could not justify is how to validate these times? scientific basis.
We have records for two years, and have never had any deviation.
I am very confused.
I appreciate your input.
#2
Posted 06 July 2022 - 04:40 PM
Hello, welcome to the forum. Hope, the attached would give you some idea.
Attached Files
Thanked by 3 Members:
|
|
#3
Posted 06 July 2022 - 05:02 PM
How did you determine your ATP parameters for clean enough
Do you perform a full wet clean daily? If so, why did you chose weekly for ATP?
If the auditor asked specifically about VALIDATION, they are looking for a report that explains WHY you do your checks at the frequencies you do, not just what you do
Please stop referring to me as Sir/sirs
#4
Posted 06 July 2022 - 05:29 PM
At the beginning, ATP was performed daily and, after a year, as the results were always satisfactory, it was decided to perform it once a week.
we use the chemicals recommended by Cintas supplier for food contact surfaces and Non Contact Surface. Follow the cleaning and sanitization schedule.
#5
Posted 06 July 2022 - 06:14 PM
So you do not have a summary of the sanitation process and testing that would work as a validation?
Please stop referring to me as Sir/sirs
Thanked by 1 Member:
|
|
#6
Posted 06 July 2022 - 06:22 PM
Yes, we have the cleaning and sanitation procedure and records for the last two years, but this is not sufficient for the auditor.
He wants to know how each week's decision was made for the ATP and Microbiological Test annually
#7
Posted 06 July 2022 - 06:37 PM
Yes, we have the cleaning and sanitation procedure and records for the last two years, but this is not sufficient for the auditor.
He wants to know how each week's decision was made for the ATP and Microbiological Test annually
I don't think you need a scientific base for your decision as it's based on your historical data of testing results. Just write a document explaining your decision: no negative swabbing results for the 2-year period, no customer complaints concerning the matter, chemicals are used at correct concentration, no deviations regarding cleaning/sanitation, no negative observations during pre-ops, correlate your decision to your GFSI scheme and/or regulatory requirements, etc., etc. Pour more water into your barrel:)
Thanked by 1 Member:
|
|
#8
Posted 07 July 2022 - 11:33 PM
Hello everyone, I need your guidance, in a recent audit the auditor has asked me to justify how I perform the validation of cleanliness in the packaging area (Our company is only dedicated to the repackaging of processed foods).My explanation is that our procedures are:- Using an ATP once a week on all contact surfaces and monthly for non-contact surfaces.- Microbiological test (Enterobacteria test) once a year on all surfaces.The question that the auditor asked me and that I could not justify is how to validate these times? scientific basis.We have records for two years, and have never had any deviation.I am very confused.I appreciate your input.
Hi esperanza,
What is the Standard which you are being audited for ? Local standard, BRC, SQF etc ?
(Sounds like a BRC risk assessment query.)
Kind Regards,
Charles.C
#9
Posted 15 July 2022 - 02:39 PM
What you basically did was verify your sanitation, and not validate. To validate your need to do swabbing and micro testing of equipment and materials pre-sanitation and then again post-sanitation.
You should see ATP pre-sanitation of course and that will be your baseline. Passing of ATP (whatever limits you set) will show the cleaning is effective and thus validated. Same with the the micro results.
Further atp and micro tests in a set frequency serve as verification.
You should re-validate anytime there is a change to cleaning procedures, cleaning supplies, and/or equipment.
1 user(s) are reading this topic
0 members, 1 guests, 0 anonymous users