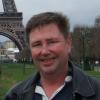
Best Answer Tony-C, 16 July 2022 - 04:17 AM
Hi Josharp186,
SQF Requirements are specified in Clause 2.1.2 Management Review (Mandatory)
2.1.2.1 The SQF System shall be reviewed by senior site management at least annually and include:
iv. Corrective and preventative actions and trends in findings from internal and external audits, customer complaints, and verification and validation activities;
v. Hazard and risk management system; and
vi. Follow-up action items from previous management reviews.
Your management review should include a review of activities under 2.5.1 Validation and Effectiveness (Mandatory) and 2.5.2 Verification Activities (Mandatory)
So, review a summary of activities that confirm Good Manufacturing Practices are achieving the required results; This could be review of inspections or relevant test results. Critical food safety limits re-validation; and any validation of changes to the processes or procedures. This could be review of extra testing or confirmation of original validation information such as legislation.
Verification activities will include audits and inspection. Review a summary of compliance, non-conformances, corrective actions as a result of verification activities and completion of audit/inspections performance vs. schedule.
Kind regards,
Tony
