- Home
- Sponsors
- Forums
- Members ˅
- Resources ˅
- Files
- FAQ ˅
- Jobs
-
Webinars ˅
- Upcoming Food Safety Fridays
- Upcoming Hot Topics from Sponsors
- Recorded Food Safety Fridays
- Recorded Food Safety Essentials
- Recorded Hot Topics from Sponsors
- Food Safety Live 2013
- Food Safety Live 2014
- Food Safety Live 2015
- Food Safety Live 2016
- Food Safety Live 2017
- Food Safety Live 2018
- Food Safety Live 2019
- Food Safety Live 2020
- Food Safety Live 2021
- Training ˅
- Links
- Store ˅
- More
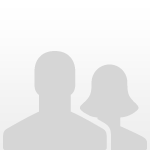
Spending money on micro and compressed air testing for SQF
Started by adam4649, Oct 19 2015 07:20 PM
7 replies to this topic
#1
Posted 19 October 2015 - 07:20 PM
I am working on a facility that produces frozen bread dough and management is not willing to spend the money in order to get microbiological and compressed air quality testing done. I am worried about getting someone sick or even worse. I have done environmental testing, which has some back clean, but there has been no finished product testing ever for this facility. We have been here 20+ years, and have only gotten SQF in the past 3. Because we didn't have the testing for the past three SQFs, management doesn't seem willing to foot the cost for all the testing.
Any advice?
#2
Posted 19 October 2015 - 07:55 PM
Hi Adam,
There are companies that do this type of testing by sending you a device to capture compressed air from the source where it's used (for example a compressed air hose/nozzle to blow out dry ingredients or help dry areas where evaporation is hindered by design on equipment after a scheduled clean and sanitizing process). Trace Analytics is one company that has this capability.
Another less expensive route is to work with an accredited 3rd party lab who can sanitize relevant air nozzles in you process and direct compressed air onto the surface of a sterile sponge (aseptically of course), then run micro and examine the swab for any signs of water or oil and send you a final report.
If air is used as an ingredient in your process (I doubt that it is with frozen bread dough) it might be wise to use the first example.
Done annually these could serve as your validations, and your Maintenance Departments Preventive Maintenance program could be used a verifications (basically written records regarding the frequency of changing the air compressor filters).
SQF is pretty non-prescriptive on this topic, so as long as you have a thought out and logical validation procedure and can verify that your control(s) are effective you should be good to go.
Good luck,
esquef
Thanked by 1 Member:
|
|
#3
Posted 19 October 2015 - 08:48 PM
Hi Adam,
I assume frozen bread dough is required to be "cooked" by consumer. Presumably Low risk in auditorial eyes.
I assume you were not audited by SQF for the first 17 years.
If i understand yr post correctly, you achieved SQF certification for 3 years without doing any compresed air or product micro testing. Based on various threads here, this is a notable achievement from a purely certification POV. I deduce that SQF auditors were impressed by yr CA procedure/general hygiene.
In such cases, it is sadly not unusual for "Top Management" to place certification/financial logic before intangible fears regarding food safety.
I assume also that (a) you are occasionally (satisfactorily) vetted by official Government Inspectors from a Hygiene/haccp etc POV, (b) yr complaint record is good and (c) yr job position is secure.
Although a potential slippery slope, eg (c) above, you might consider asking the SQF Inspectors to add a minor caveat to yr audit documentation over the absence of micro. data ? (I'm amazed its not happened already).
Or perhaps you have a concern over some specific microbiological aspect ?
Kind Regards,
Charles.C
Thanked by 1 Member:
|
|
#4
Posted 20 October 2015 - 02:25 PM
Hi Adam,
There are companies that do this type of testing by sending you a device to capture compressed air from the source where it's used (for example a compressed air hose/nozzle to blow out dry ingredients or help dry areas where evaporation is hindered by design on equipment after a scheduled clean and sanitizing process). Trace Analytics is one company that has this capability.
Another less expensive route is to work with an accredited 3rd party lab who can sanitize relevant air nozzles in you process and direct compressed air onto the surface of a sterile sponge (aseptically of course), then run micro and examine the swab for any signs of water or oil and send you a final report.
If air is used as an ingredient in your process (I doubt that it is with frozen bread dough) it might be wise to use the first example.
Done annually these could serve as your validations, and your Maintenance Departments Preventive Maintenance program could be used a verifications (basically written records regarding the frequency of changing the air compressor filters).
SQF is pretty non-prescriptive on this topic, so as long as you have a thought out and logical validation procedure and can verify that your control(s) are effective you should be good to go.
Good luck,
esquef
Hi esquef,
Thank you for your reply. We have contacted Trace Analytics and because of the quote they gave us, management decided not to go through with it because we never had it done before. I'm a little worried because this will be my first audit, as I am new to this position. We had SQF before I came on. I wanted to get the testing done because of SQF 11.5.7. I'm going to the swab testing done to at least have something, so thank you for the recommendation.
We use compressed air to move flour from our silo. It's also used in cleaning the production line.
Best Regards,
Adam
Hi Adam,
I assume frozen bread dough is required to be "cooked" by consumer. Presumably Low risk in auditorial eyes.
I assume you were not audited by SQF for the first 17 years.
If i understand yr post correctly, you achieved SQF certification for 3 years without doing any compresed air or product micro testing. Based on various threads here, this is a notable achievement from a purely certification POV. I deduce that SQF auditors were impressed by yr CA procedure/general hygiene.
In such cases, it is sadly not unusual for "Top Management" to place certification/financial logic before intangible fears regarding food safety.
I assume also that (a) you are occasionally (satisfactorily) vetted by official Government Inspectors from a Hygiene/haccp etc POV, (b) yr complaint record is good and (c) yr job position is secure.
Although a potential slippery slope, eg (c) above, you might consider asking the SQF Inspectors to add a minor caveat to yr audit documentation over the absence of micro. data ? (I'm amazed its not happened already).
Or perhaps you have a concern over some specific microbiological aspect ?
Hello Charles,
Thank you for your helpful reply. Yes, we were not audited by SQF before and we only have picked it up because our customers have required it of us. I'm quite surprised we passed the previous three years with what little documentation and testing. We have been inspected by the FDA and they have been okay with our facility, however I worry due to the Food Safety Modernization Act passed last month, giving the FDA more auditing power, and with changes from HAACP to HARCP that there could be potential issues in the future.
I reviewed the previous audit and it seems that microbiological wasn't asked for. I thought it would be in SQF 2.5.6, but when I reviewed the final audit report, it wasn't mentioned as even a minor.
My concern about the microbiological is that if there was contamination in the product, we just wouldn't know. We use old dough in new batches of dough to reduce waste, so it would contaminate everything.
Best Regards,
Adam
#5
Posted 20 October 2015 - 02:36 PM
Oh, I forgot to add that while we are producing a product that requires baking, so the microorganisms would be destroyed. Internally conducted product testing has confirmed that when baked to instructions, all products finished at an internal temperature of 210-212. I am concerned about spores or possible endotoxins and exotoxins that could remain from the dead organisms.
#6
Posted 20 October 2015 - 06:57 PM
As a former SQF Registered Auditor all I can say is that you been lucky that you never got a major for not testing air lines, I can only deduce that you have had the same auditor for 3 years now, however that is the maximum time for one auditor to visit. So, on your next audit you'll have a different auditor. Regardless your company needs to test and I see there is one company on the forum that advertises this service. Most of our clients use Tri-Air out of Austin, Texas as they are very reliable and quick once your air sample kit is returned. It really is a small price to pay for peace of mind. We had the president of one company call us and say that even though we balked at paying for the service initially he was amazed by what the test turned up, so much so that a number of practices had to be changed to prevent what was found in the lines and of course what was found was also going into their frozen dough as well.
All the Best,
All Rights Reserved,
Without Prejudice,
Glenn Oster.
Glenn Oster Consulting, LLC
SQF System Development | Internal Auditor Training | eConsultant
http://glennoster.website3.me/ -- 774.563.6161
Now accepting RLUSD, XRP, XLM, XDC & Bitcoin
Blog
Thanked by 2 Members:
|
|
#7
Posted 04 November 2015 - 04:54 PM
I don't know if it will be enough but at least it would be something... When we were first faced with this dilemma of the compressed air testing we had trouble getting funding too so we did in-house testing to show we were at least doing something.
We had the air from our hoses blow into a sterile clear plastic bag for a set number of seconds, we used 30 seconds as our product zips through our lines and maybe the air would touch it for only a second or two. We then inspected the bag for any physical or chemical contaminants such as metal shavings or dust particles from pipes or oils or greases and recorded results, you want the answer to be zero contaminants found.
For micro, we aseptically added dilution buffer (we used 10 mL to keep the dilution factor low) into the bag and massaged the bag for 1 minute to loosen any microbes that might be present and plated the liquid. You can plate on whatever media you choose; we tested for APC, coliform, yeast and mold on Petrifilm plates. We did find one line that had some APC growth higher than the other lines so we changed out the hose for that one line, as all our compressed air comes from the same source, and the follow up tests were good. I do not know what an acceptable count would be for your products but we have a limit for APC similar to a surface count limit on our product and then zero for coliform, yeast and mold.
Thanked by 1 Member:
|
|
#8
Posted 04 November 2015 - 06:03 PM
Hi Lee Ann,
Actually there are standardized procedures for the evaluation of compressed air quality. And limits regarding contaminants, other than microbiological . And SQF recommended filtration unit installation.
These are i think all described in the SQF Guidelines. And discussed in depth in other threads on this Forum.
I'm surprised that SQF were satisfied with yr ad-hoc methodologies. But not that surprised.
Kind Regards,
Charles.C
Also tagged with one or more of these keywords: sqf, management, testing, test, microbiological, air, purity
Government Regulatory →
USDA - United States Department of Agriculture →
Environmental Monitoring Program Concerns at USDA-Regulated Meat FacilityStarted by BobbyLow859, 01 Jul 2025 ![]() |
|
![]() |
|
Global Food Safety Standards →
General Food Safety Standards →
USDA Registration Needed for Fulfillment of Meat Products?Started by Renee Johnson, 26 Jun 2025 ![]() |
|
![]() |
|
Global Food Safety Standards →
SQF Storage & Distribution →
Using Uncertified External Warehouse for SQF Storage: Risks and ComplianceStarted by MSPShawn, 22 May 2025 ![]() |
|
![]() |
|
Food Safety Topics →
Auditing →
Food GMP Facility Audit Number – What Is It?Started by cmlidestri, 06 May 2025 ![]() |
|
![]() |
|
Global Food Safety Standards →
SQF Food →
SQF V10 changesStarted by Scampi, 30 Apr 2025 ![]() |
|
![]() |
0 user(s) are reading this topic
0 members, 0 guests, 0 anonymous users