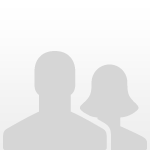
Best Answer Ligita012, 20 November 2021 - 05:45 PM
Magnets are a poor CCP (if that is what you are stating). I have seen one validation study that is next to impossible to achieve. Plus the issue that you have. as usual Charles is on the money.
In general, the magnet is metal detection and removal /tool. It helps identify possible FM issues in the plant. As such, you should examine (as you are) and take actions on adverse findings (which you are not).
You could deem dust to be acceptable and not require investigation (if this makes sense with your equipment). Or set a limit as to the amount that requires investigation/capa. It may be that any dust requires a investigation & capa.
Pieces that could be considered a food safety risk (wires, pieces larger than "X", pieces that indicated equipment failure) would always require a investigation and corrective / preventative actions. These are just examples of things I have seen or done. You will have to determine what makes sense for your operation.
Strength of magnets should be checked annually (gauss or pull strength test) to ensure they remain effective.
Dear, your answer is what I was searching for, what is acceptable, what is not.
Metal dust is acceptable. Larger pieces, bigger amount of dust than usually or wires-not acceptable (needs corrective actions). For me now is more clear. Thank you very much for your help.
